A laboratory furnace is a critical tool used in high-temperature applications, ranging from materials testing and sintering to heat treatment and annealing. These furnaces are designed to withstand extreme temperatures and provide precise control, ensuring consistent results in various scientific and industrial fields such as ceramics, metallurgy, chemistry, and electronics. In this article, we will explore the types of laboratory furnaces, their key features, common applications, and tips for choosing the right furnace for your needs.
Types of Laboratory Furnaces
Laboratory furnaces come in various forms, each designed to handle specific applications. Below are the most common types of furnaces used in laboratories today:
1. Muffle Furnace
The muffle furnace is one of the most widely used laboratory furnaces. It features a high-temperature heating chamber surrounded by insulation, which allows for a controlled and clean environment for heat treatment. This furnace is ideal for processes like sintering, ash content determination, and annealing. Muffle furnaces are often used in metallurgy, ceramics, and chemistry for testing the purity of materials and conducting thermal decomposition.
2. Tube Furnace
A tube furnace consists of a cylindrical chamber (tube) that is heated by elements placed around it. These furnaces are ideal for processes requiring a controlled atmosphere or vacuum conditions, such as sintering and crystallization. Tube furnaces are commonly used in chemistry and materials science for testing gases and solid-state reactions.
3. Box Furnace
Box furnaces offer a large, enclosed chamber where materials can be heated uniformly. These furnaces are versatile, providing excellent heat distribution and are often used for ceramic firing, metal heat treatment, and composite material processing.
4. Ashing Furnace
An ashing furnace is used for burning off organic material from samples to determine the amount of inorganic material (ash) present. These furnaces are commonly used in chemical analysis, particularly in industries like food processing, agriculture, and pharmaceuticals, where precise measurement of mineral content is critical.
5. Vacuum Furnace
A vacuum furnace operates by removing air and other gases from the heating chamber, creating a vacuum. This prevents oxidation and contamination during processes like sintering and heat treatment of sensitive materials such as metals, alloys, and ceramics. Vacuum furnaces are widely used in electronics manufacturing, aerospace, and material science applications.
Key Features of Laboratory Furnaces
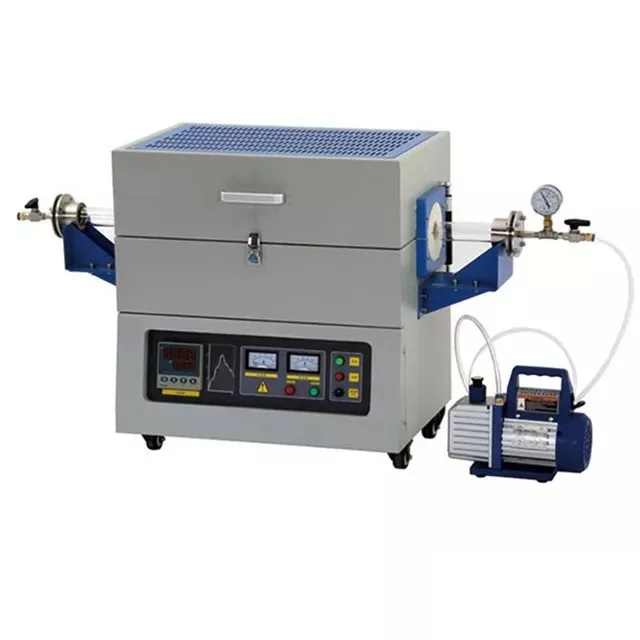
When selecting a laboratory furnace, it is important to consider the following key features to ensure it meets the specific needs of your applications:
1. Temperature Range
The temperature range is the most critical feature of any laboratory furnace. Some furnaces operate at temperatures as high as 1800°C or more, making them suitable for applications like ceramics processing and metal annealing. Choose a furnace with a temperature range that aligns with your processes.
2. Precision Temperature Control
Precise temperature control is essential for maintaining consistent and accurate results. Most modern furnaces feature digital controls and programmable settings that allow users to create specific heating profiles for their materials. This is especially important in processes like sintering and heat treatment.
3. Heating Elements
The type of heating element used in the furnace will determine its efficiency and durability. Silicon carbide, molybdenum disilicide, and graphite heating elements are commonly used in high-temperature furnaces, each offering specific benefits based on the required application.
4. Atmosphere Control
For processes like vacuum heat treatment or working with sensitive materials, a laboratory furnace that allows for atmosphere control (i.e., the ability to introduce an inert gas or create a vacuum) is vital. This prevents oxidation and ensures the integrity of the material.
5. Size and Capacity
The size and capacity of the furnace are important considerations depending on the volume of materials you need to process. Box furnaces typically offer more capacity, while tube furnaces are ideal for smaller, more precise applications.
6. Energy Efficiency
Choosing an energy-efficient furnace can reduce operational costs over time, especially if it is used for long-duration or frequent high-temperature processes. Many modern furnaces are designed to conserve energy without sacrificing performance.
Applications of Laboratory Furnaces
Laboratory furnaces are used in a wide range of industries and scientific research fields. Here are some of the most common applications:
1. Sintering of Ceramics and Metals
Sintering is a process used to compact and form materials by applying heat without melting them. Laboratory furnaces are used in the ceramics and metallurgy industries to sinter powders into solid materials.
2. Annealing
Annealing involves heating metals, alloys, or glass to remove internal stresses, improve ductility, or alter their physical properties. High-temperature laboratory furnaces are used to perform precise annealing operations in fields like aerospace, automotive, and electronics.
3. Heat Treatment of Metals
Heat treatment processes such as hardening, tempering, and stress relieving are performed in laboratory furnaces. These processes are essential for enhancing the mechanical properties of metals used in industries like engineering and manufacturing.
4. Material Testing and Research
Laboratory furnaces are commonly used in research and development for testing the behavior of materials under extreme temperatures. This includes testing for thermal expansion, degradation, and chemical reactions in fields like materials science and chemistry.
5. Thermal Decomposition and Ashing
Ashing furnaces are used in laboratories to thermally decompose organic materials, leaving behind an inorganic residue (ash). This technique is widely used in chemical analysis and food processing for determining the composition of materials.
Maintenance Tips for Laboratory Furnaces
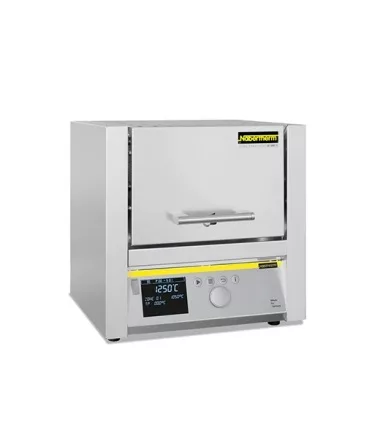
To ensure that your laboratory furnace continues to operate efficiently and reliably, follow these maintenance tips:
- Regular Calibration: Ensure the furnace is regularly calibrated to maintain accurate temperature settings. Calibration is particularly important in processes requiring high precision, such as material testing.
- Clean the Chamber: Keep the interior of the furnace clean by removing any residue or buildup from previous processes. This prevents contamination and ensures uniform heating.
- Inspect Heating Elements: Regularly check the condition of the heating elements and replace them as necessary to avoid uneven heating or furnace malfunction.
- Check for Proper Ventilation: Ensure the furnace has proper ventilation to prevent overheating and maintain safe operating conditions.
- Monitor Power Consumption: Track energy consumption and ensure that the furnace is running efficiently. An increase in energy usage could signal that maintenance is required.
Conclusion: Enhancing High-Temperature Processes with the Right Laboratory Furnace
A laboratory furnace is an essential tool for high-temperature processes, offering precise temperature control, durability, and flexibility in a wide range of applications, from sintering and heat treatment to material testing. Understanding the various types of furnaces and their specific applications can help you choose the right furnace for your laboratory, ensuring accurate and reliable results.